網上版請按此
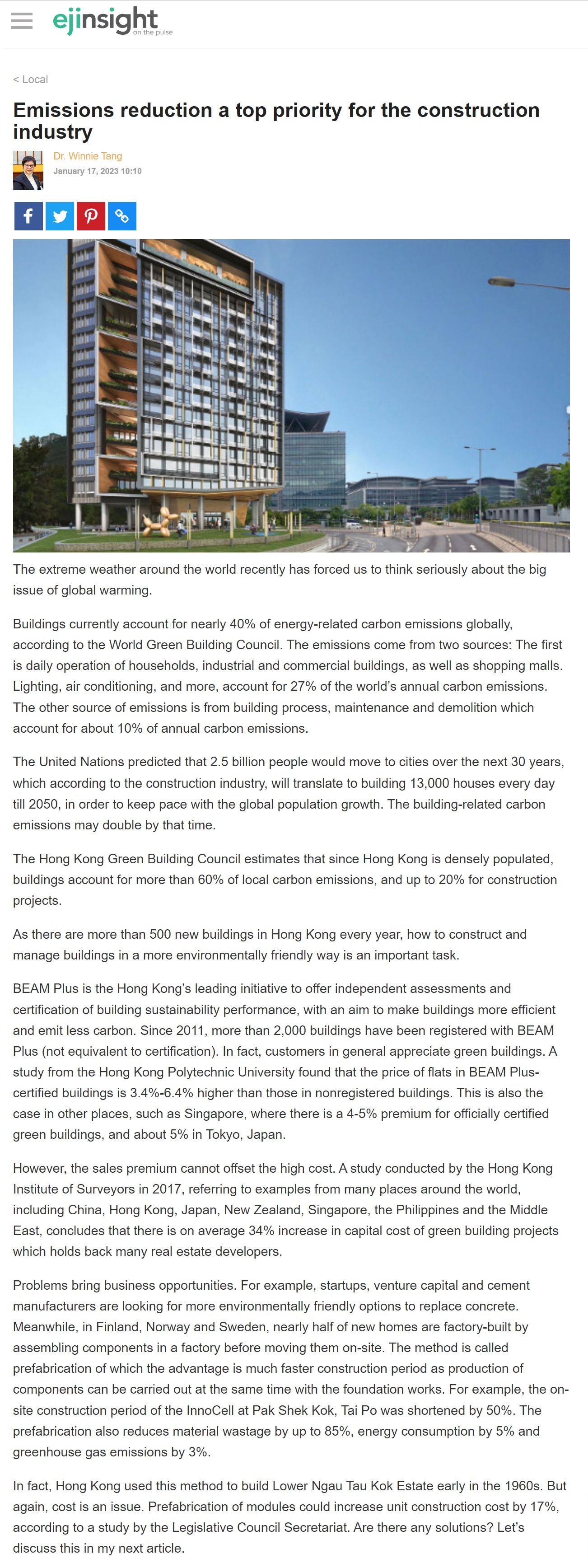
Emissions reduction a top priority for the construction industry
The extreme weather around the world recently has forced us to think seriously about the big issue of global warming.
Buildings currently account for nearly 40% of energy-related carbon emissions globally, according to the World Green Building Council. The emissions come from two sources: The first is daily operation of households, industrial and commercial buildings, as well as shopping malls. Lighting, air conditioning, and more, account for 27% of the world's annual carbon emissions. The other source of emissions is from building process, maintenance and demolition which account for about 10% of annual carbon emissions.
The United Nations predicted that 2.5 billion people would move to cities over the next 30 years, which according to the construction industry, will translate to building 13,000 houses every day till 2050, in order to keep pace with the global population growth. The building-related carbon emissions may double by that time.
The Hong Kong Green Building Council estimates that since Hong Kong is densely populated, buildings account for more than 60% of local carbon emissions, and up to 20% for construction projects.
As there are more than 500 new buildings in Hong Kong every year, how to construct and manage buildings in a more environmentally friendly way is an important task.
BEAM Plus is the Hong Kong's leading initiative to offer independent assessments and certification of building sustainability performance, with an aim to make buildings more efficient and emit less carbon. Since 2011, more than 2,000 buildings have been registered with BEAM Plus (not equivalent to certification). In fact, customers in general appreciate green buildings. A study from the Hong Kong Polytechnic University found that the price of flats in BEAM Plus-certified buildings is 3.4%-6.4% higher than those in nonregistered buildings. This is also the case in other places, such as Singapore, where there is a 4-5% premium for officially certified green buildings, and about 5% in Tokyo, Japan.
However, the sales premium cannot offset the high cost. A study conducted by the Hong Kong Institute of Surveyors in 2017, referring to examples from many places around the world, including China, Hong Kong, Japan, New Zealand, Singapore, the Philippines and the Middle East, concludes that there is on average 34% increase in capital cost of green building projects which holds back many real estate developers.
Problems bring business opportunities. For example, startups, venture capital and cement manufacturers are looking for more environmentally friendly options to replace concrete. Meanwhile, in Finland, Norway and Sweden, nearly half of new homes are factory-built by assembling components in a factory before moving them on-site. The method is called prefabrication of which the advantage is much faster construction period as production of components can be carried out at the same time with the foundation works. For example, the on-site construction period of the InnoCell at Pak Shek Kok, Tai Po was shortened by 50%. The prefabrication also reduces material wastage by up to 85%, energy consumption by 5% and greenhouse gas emissions by 3%.
In fact, Hong Kong used this method to build Lower Ngau Tau Kok Estate early in the 1960s. But again, cost is an issue. Prefabrication of modules could increase unit construction cost by 17%, according to a study by the Legislative Council Secretariat. Are there any solutions? Let's discuss this in my next article.
Dr. Winnie Tang
Adjunct Professor, Department of Computer Science, Faculty of Engineering; Department of Geography, Faculty of Social Sciences; and Faculty of Architecture, The University of Hong Kong